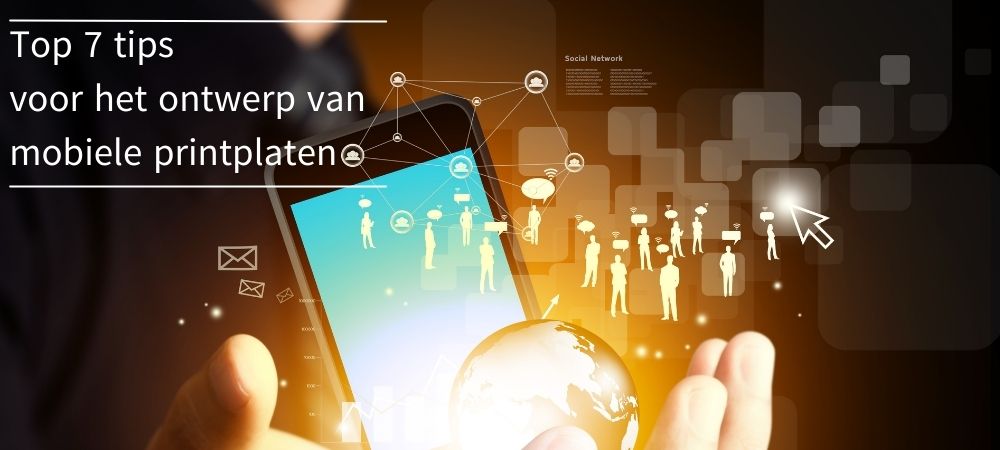
De geleidelijke toename van functies die geïntegreerd zijn in de nieuwste generatie mobiele apparaten, stelt steeds hogere eisen aan het ontwerp van printplaten. Wi-Fi- en Bluetooth-connectiviteit, ondersteuning van 4G- en 5G-mobiele netwerken, integratie met een steeds toenemend aantal sensoren vormen ongekende technologische uitdagingen voor elektronica-ontwerpers. Mobiele toestellen, te beginnen met smartphones, evolueren naar meer intelligentie, miniaturisatie en multifunctionaliteit, wat steeds complexere printplaten vereist die aan deze eisen kunnen voldoen (de door de markt opgelegde trend is om steeds dunnere toestellen te hebben, met diktes die gewoonlijk minder dan een centimeter bedragen).
Technische uitdagingen
De ontwikkelingstrend van de huidige smartphones vereist noodzakelijkerwijs meerlaagse printplaten (bestaande uit 10 of meer lagen) om het moederbord te maken en een of meer printplaten met een kleiner aantal lagen voor hulpkaarten, eventueel gemaakt met stijve-flexibele printplaten. Het steeds ruimere gebruik van SiP-componenten (System-in-Package) en meerkernige SoC's (System-on-Chip), die ook verkrijgbaar zijn met een 64-bit architectuur, alsmede de verkleining van de pinafstand van 0,4 mm tot 0,35 mm zullen de groei van het aantal lagen waarschijnlijk tegengaan, zo niet zelfs doen afnemen.
Ontwerpers van mobiele printplaten moeten vanaf de eerste fasen van de ontwikkeling veel aandacht besteden aan de technologische aspecten. De belangrijkste factoren waarmee rekening moet worden gehouden bij het ontwerpen van deze klasse printplaten zijn:
- het bepalen van de lay-out van de printplaat, de positioneringsgaten en vaste merktekens die nodig zijn voor automatische productie en assemblage
- het bepalen van het paneel dat vereist is in de productiefase van de printplaat
- het selecteren van de materialen die worden gebruikt voor de substraten, het selecteren van de juiste componenten en hun verpakking
- het positioneren van de componenten en relatieve afstand ertussen
1 – Lay-out
Het positioneren moet beginnen met de componenten met een hoger vermogen, die zo dicht mogelijk bij de onderdelen moeten worden geplaatst die hen vergezellen, op een zodanige wijze dat de kortst mogelijke hoge-stroomsporen ontstaan. Zij moeten ook een bepaalde minimumafstand houden tot de sporen waarover de hoge-snelheidssignalen lopen, aangezien deze gevoeliger zijn voor storingen en overspraakverschijnselen.
Ter indicatie, voor de plaatsing van de componenten kunt u in de volgende volgorde te werk gaan: connectoren, voedingscomponenten, gevoelige componenten, kritische componenten, resterend deel van de componenten. Alle soortgelijke componenten moeten in dezelfde richting worden georiënteerd om de kans op soldeerproblemen te verkleinen. Plaats aan de gesoldeerde kant van de printplaat geen andere componenten in de buurt van de doorvoergatklemmen (PTH), die zich aan de andere kant van de printplaat bevinden. Componenten voor opbouwmontage (SMD's) moeten aan dezelfde kant van de printplaat worden geconcentreerd; dezelfde regel moet worden toegepast op PTH-componenten, wat de assemblage vereenvoudigt en de benodigde tijd verkort.
Ga na het positioneren van de componenten over tot de routering van de sporen voor de voeding, de signalen, en de aarding. De sporen moeten met voorrang worden gerouteerd op basis van de vermogensniveaus en de gevoeligheid voor ruis en interferentie. De voedingscomponenten moeten worden geaard of geaard voor een betere warmtedissipatie, terwijl de sporen die signalen geleiden zo kort en recht mogelijk moeten zijn en niet over lange afstanden parallel mogen lopen om koppelingsverschijnselen te voorkomen. Ontkoppelingscondensatoren moeten dicht bij (of onder) de voedingspinnen worden geplaatst, zodat zij eventuele valse stroompieken kunnen absorberen.
Sporen met signalen die een hoge mate van isolatie vereisen, moeten op afzonderlijke lagen worden gerouteerd, mogelijk orthogonaal ten opzichte van elkaar met een aardingsvlak ertussen. De orthogonale positionering van de sporen minimaliseert de capacitieve koppeling, terwijl het aardingsvlak voor elektrische afscherming zorgt. Deze techniek wordt op grote schaal gebruikt om sporen met gecontroleerde impedantie te verkrijgen, waarbij de karakteristieke impedantie op elk punt van het spoor constant blijft (bijvoorbeeld 50Ω). Twee zeer gangbare soorten impedantiegeregelde sporen zijn microstrips en striplijnen die, ondanks verschillende geometrische structuren, vergelijkbare resultaten opleveren. De impedantieregeling, die kan worden uitgevoerd met een van de vele online beschikbare hulpmiddelen, houdt vaak in dat de lengte van de sporen in evenwicht moet worden gebracht. In extreme gevallen kan dit de invoering van passende ‘serpentines’ op de printplaat vereisen, zoals getoond in figuur 1.
Figuur 1: aanbrengen van ‘serpentines’ om de spoorlengte in evenwicht te brengen
2 – Scheiding
Het RF-gedeelte van een mobiele printplaat moet naar behoren worden gescheiden en geïsoleerd van de voedingsgedeelten en van de digitale of analoge laagvermogensgedeelten. Gevoelige analoge signalen moeten ook zo ver mogelijk verwijderd worden gehouden van digitale signalen met hoge snelheid en van RF-signalen. Digitale en analoge signalen moeten ook elk hun eigen aardverbindingen hebben.
Analoge en digitale schakelingen moeten, waar mogelijk, gescheiden worden gehouden. De snelle opgaande flanken van digitale signalen kunnen namelijk stroompieken veroorzaken en ruis genereren, twee factoren die mogelijk analoge schakelingen kunnen beschadigen. Figuur 2 toont een voorbeeld van hoe de scheiding tussen het analoge en digitale gedeelte van een printplaat kan worden uitgevoerd.
Figuur 2: scheiding tussen het analoge en digitale gedeelte (Bron: Altium)
3 – Via’s en vaste merktekens
Hoge-stroomsporen, vooral deze die meerdere lagen doorkruisen, moeten minstens twee tot vier via-gaten bevatten. Dat verbetert de warmtedissipatie en vermindert zowel inductie- als weerstandsverlies. Door grotere gaten te gebruiken kan de printplaat hogere stromen weerstaan en wordt de warmtegeleiding verbeterd. Voor hoge-stroomsporen is het ook beter om meerdere gaten te gebruiken in plaats van één enkel gat.
Over het algemeen moet elke zijde van de printplaat ten minste twee vaste merktekens hebben. Deze moeten rond van vorm zijn met een diameter van 1 mm (40 mil). De kleur van de vaste merktekens moet dezelfde zijn als die van de interne achtergrond, zodat ze compatibel blijven met de kopercoating.
4 – Thermisch beheer
Thermisch beheer is een belangrijk aspect dat bijzondere aandacht verdient, omdat een onjuiste warmtehuishouding de printplaat kan aantasten of zelfs beschadigen. De ontwerper moet daarom (door de relevante datasheets te raadplegen) de thermische weerstandswaarden voor elk component beoordelen en bepalen welke componenten de meeste warmte afvoeren. Vervolgens moet ervoor worden gezorgd dat de meest kritische componenten op een voldoende grote afstand worden geplaatst van de componenten die warmte genereren.
Het gebruik van grotere sporen is de eerste truc om warmteontwikkeling tegen te gaan. Vermogenscomponenten, die aan grotere oververhitting onderhevig zijn, moeten in het midden van de plaat worden geplaatst om de warmte te helpen afvoeren, terwijl ze gescheiden blijven van andere hete componenten. Als de grootte van het ontwerp het toelaat, moeten eventueel ook koelventilatoren, koellichamen, massieve aardings- en voedingsvlakken, en een voldoende aantal thermische doorgangen worden overwogen. Het kan ook nodig zijn de dikte van de laminaten te vergroten of andere materialen te gebruiken met een betere sterkte en warmtedissipatie.
5 – Aardingsvlakken
Een aardingsvlak biedt een gemeenschappelijke referentiespanning, zorgt voor afscherming, maakt warmtedissipatie mogelijk en vermindert parasitaire inductie (hoewel de parasitaire capaciteit toeneemt). Idealiter zou elke printplaat ten minste één laag volledig moeten hebben gewijd aan het aardingsvlak. De beste resultaten worden verkregen wanneer dit vlak massief is, d.w.z. zonder onderbrekingen.
Aangezien het aardingsvlak meestal een groot oppervlak van de printplaat inneemt, is zijn weerstand minimaal. Bij lage frequenties zal de stroom het pad met de laagste weerstand volgen, terwijl bij hoge frequenties de stroom het pad met de laagste impedantie zal volgen. De aardings- en voedingsvlakken moeten symmetrisch, gecentreerd en in de binnenste lagen van de printplaat worden aangebracht.
6 – Materialen
De technologie die wordt gebruikt voor de fabricage van meerlaagse printplaten wordt op grote schaal gebruikt in medische toepassingen. Bij de fabricage van een meerlaage printplaat wordt een subtractief proces toegepast om de lagen van de printplaat te genereren. De onderlinge verbinding tussen de lagen wordt verkregen door fasen van lamineren, mechanisch boren, chemisch verkoperen en verkoperen. Het proces wordt voltooid met de vervaardiging van het soldeermasker, de beschermende coating van de printplaat (conforme coating) en de zeefdruk.
De huidige meerlaagse printplaten zijn uitzonderlijk dun, hebben een zeer kleine spoorbreedte en -afstand, en worden gekenmerkt door een bijzonder hoge component- en spoordichtheid.
7 – Paneel
Een goede PCB ontwerper moet in de ontwikkeling ook een paneelontwerp voor de assemblagefase opnemen. Zodra het printplaatontwerp is voltooid, bestaat de volgende stap uit het verzenden van de printplaatgerelateerde informatie naar een productiebedrijf, samen met een specificatie van het paneelontwerp om ervoor te zorgen dat het printplaatontvangstformaat is zoals bedoeld. Dergelijke informatie moet het volgende omvatten:
- de maximale paneelgrootte die door de productiemachines kan worden beheerd
- aanvullende vaste merktekens, zodat de visuele uitlijningssystemen van de machine precies weten waar de printplaat zich bevindt. De standaardpraktijk bestaat erin drie vaste merktekens op het paneel aan te brengen in drie van de vier hoeken aan weerszijden van de printplaat, zodat de machine kan bepalen of de printplaat al dan niet correct is geladen
- indien de machine dit vereist, speciale gaten (gereedschapsgaten) aanbrengen in de buurt van de randen om de verwerking van de printplaat mogelijk te maken
- de hoeken van het paneel zo buigen dat wanneer de printplaatpanelen vacuüm worden verpakt, de hoeken de verzegeling niet kunnen verbreken
Figuur 3 toont een voorbeeld van een correct ontworpen paneel.