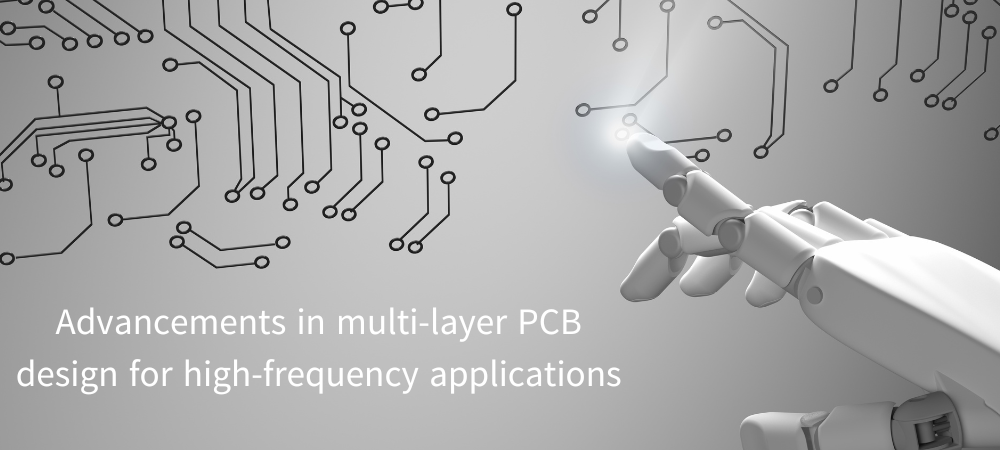
The need for high-performance devices with expanded functionality is increasing in the ever-changing field of electronics. The need for printed circuit board (PCB) technology has resulted in notable progress, particularly in the domain of high-frequency applications. The utilization of multi-layer PCB design has become a crucial solution in order to satisfy the rigorous demands of these applications.
This article explores the advantages, challenges, and feasibility of multi-layer PCBs specifically designed for high-frequency applications.
The advent of multi-layer PCBs
Historically, printed circuit boards were primarily characterized by their single or double-layered structure, which imposed constraints on their suitability for high-frequency applications owing to signal deterioration and electromagnetic interference (EMI). Nevertheless, the introduction of multi-layered printed circuit boards has resulted in notable advancements in signal integrity, electromagnetic interference (EMI) mitigation, and overall performance.
Multi-layered PCBs (Figure 1) consist of numerous conductive layers that are separated by insulating substrates. This design enables the transmission of signals and power planes in a sophisticated manner.
Figure 1: Internal structure of a multi-layer PCB
Multi-layer printed circuit boards (PCBs) are distinguished from their single or double-layer counterparts by the presence of three or more conductive layers that are separated by insulating material, commonly known as dielectric layers. The interconnection of these layers is facilitated by vias, which are minuscule conductive passageways that facilitate communication between distinct layers. The complicated design of multi-layer PCBs enables a greater concentration of components and intricate circuitry, rendering them essential for state-of-the-art technology.
Multilayer PCBs typically exhibit a high degree of rigidity due to the inherent challenge of achieving multiple layers within a flexible PCB structure. Electrical connections between layers are established through the utilization of several types of vias (figure 2), including blind and buried vias.
The configuration entails the placement of two layers on the surface to establish a connection between the printed circuit board (PCB) and the external environment. In general, the density of layers in printed circuit boards (PCBs) is even. This is primarily due to the susceptibility of odd numbers to issues such as warping.
The number of layers typically varies depending on the specific application, typically falling within the range of four to twelve layers.
Typically, the majority of applications necessitate a minimum of four and a maximum of eight layers. In contrast, apps such as smartphones predominantly employ a total of twelve layers.
Figure 2: Vias are used to interconnect layers (Source: Altium)
Main applications
Multi-layer PCBs are used in a wide range of electronic applications (Figure 3), including:
- Consumer electronics, where multi-layer PCBs play a fundamental role providing the necessary power and signals for a wide range of products such as smartphones, tablets, gaming consoles, and wearable devices. The sleek and portable electronics that we depend on daily are attributed to their compact design and high component density
- In the field of telecommunications, the utilization of multi-layer PCBs facilitates the smooth transmission of voice, data, and video signals across networks, thereby guaranteeing dependable and effective communication
- Industrial control systems heavily depend on multi-layer printed circuit boards (PCBs) due to their capacity to effectively manage intricate control systems, monitoring mechanisms, and automation procedures. Machine control panels, robotics, and industrial automation rely on them as their fundamental support system
- Multi-layer PCBs are also relevant for medical devices, since they are crucial for ensuring precision, dependability, and compactness. Diagnostic equipment, patient monitoring systems, and life-saving medical devices are significantly influenced by their important role.
Figure 3: A complex PCB requires a multi-layer design (Source: Altium)
Benefits and advantages
Multi-layer PCBs provide several benefits and advantages in high-frequency applications, including:
- Enhanced signal integrity: Multi-layered PCBs facilitate controlled impedance routing, minimizing signal distortion and ensuring reliable transmission of high-frequency signals. The lower signal interference of multi-layer printed circuit boards result in improved performance, velocity, and dependability
- Reduced EMI: By utilizing dedicated ground and power planes, multi-layered PCBs effectively suppress EMI, thereby enhancing system reliability and minimizing interference with neighboring circuits
- Compact Design: With the ability to accommodate more components and complex routing schemes, multi-layered PCBs enable compact designs, crucial for space-constrained applications such as mobile devices and aerospace systems.
- Improved Thermal Management: Multi-layered PCBs offer efficient heat dissipation through the integration of thermal vias and strategically placed copper layers, enhancing the reliability and lifespan of high-power components.
- Design Flexibility: The versatility of multi-layered PCBs allows for greater design flexibility, enabling engineers to optimize performance parameters such as impedance matching, signal propagation delay, and power distribution.
Disadvantages
One of the main drawbacks associated with multilayer printed circuit boards is their higher cost compared to single and double-layer PCBs throughout all stages of the manufacturing process. The higher cost is mainly associated with the specialized equipment required for their production.
The manufacturing is also more complex, as the production of multilayer PCBs necessitates a significantly longer design period and meticulous manufacturing methods compared to other types of PCBs. Manufacturing Complexity: The fabrication of multi-layered PCBs demands sophisticated manufacturing processes, including precise layer alignment, controlled impedance routing, and stringent quality control measures, leading to increased production costs and longer lead times.
Multilayer PCBs necessitate thorough pre-design and, therefore, proficient engineers are needed for its development. The production of each board necessitates a substantial amount of time, leading to increased labor expenses. Moreover, it may result in extended time intervals between the placement of an order and the receipt of the product, which can be a challenge in some situations.
Nevertheless, these concerns do not undermine the efficacy of multilayer printed circuit boards (PCBs). Although multilayer PCBs are often more expensive than single-layer PCBs, they offer numerous advantages compared to this particular form of printed circuit board.
As electronic devices continue to shrink in size and increase in power density, effective thermal management becomes critical in multi-layered PCBs, necessitating innovative solutions to mitigate thermal hotspots and ensure optimal performance. Additionally, validating the performance of multi-layered PCB designs requires comprehensive testing methodologies, including simulation, prototyping, and compliance testing, to ensure compliance with industry standards and specifications.
Multilayer PCB design tips
When creating a multi-layer printed circuit board (PCB) for high-frequency applications, several useful suggestions are usually useful.
In order to mitigate the issues in multilayer PCB design, the primary area of emphasis typically revolves around the stackup. When making judgments about layer stackup, it is important to take into account factors such as functionality, manufacturing, and deployment.
Begin by optimizing the dimensions of the board, as this will influence decisions regarding other characteristics. When determining the ideal board size, take into account the following factors:
- The number of components to be housed on the board
- The size of these components
- Where the board will be installed
- The manufacturing partner's allowances for spacing, clearances, and drill holes
Once the number of layers has been decided, the selection of vias, whether blind, through hole, buried or via in pad shall be performed. This aspect affects manufacturing complexity, hence PCB quality.
In the multilayer PCB design section, PCB design software is an essential part of the design process. It helps designers to generate the structure of the PCB’s mechanical and wiring connection from the netlist, and to place this connection structure on multilayers and to generate computer-aided design files. This CAD is essential in manufacturing the PCB. There are several PCB design software options that you can use to design your multilayer PCB. However, some few are used more widely than others, especially because of their simpler interface, among other reasons.
DFM, whose objective is to create product parts and components that facilitate manufacturing, shall also be considered. The objective is to attain high-quality products at reduced expenses. Consequently, it entails streamlining, enhancing, and perfecting the product's design. DFM should be conducted in a timely manner prior to commencing tooling. It is imperative to involve all stakeholders in the DFM. The involvement of several stakeholders, including designers, engineers, contract manufacturers, material suppliers, and mold builders, is crucial. By doing so, possible issues with the design can be mitigated.
Manufacturability
Manufacturing multi-layered PCBs for high-frequency applications involves several key steps:
- Design and Layout: Engineers utilize specialized PCB design software to create the layout, considering factors such as signal integrity, thermal management, and EMI mitigation.
- Material Selection: High-quality materials with low dielectric constant and loss tangent are chosen to minimize signal loss and maintain high-frequency performance.
- Layer Stackup Planning: The layer stackup is carefully planned to optimize signal routing, impedance matching, and thermal dissipation, considering factors such as signal frequency, board thickness, and copper thickness.
- Fabrication and Assembly: Advanced fabrication techniques such as laser drilling, sequential lamination, and controlled impedance etching are employed to manufacture multi-layered PCBs with precision and reliability.
- Testing and Quality Assurance: Rigorous testing procedures, including signal integrity analysis, impedance measurements, thermal imaging, and EMI testing, are conducted to ensure the performance, reliability, and compliance of multi-layered PCBs with industry standards and specifications.
Conclusion
The evolution of multi-layered PCB design has revolutionized the field of high-frequency electronics, enabling the development of sophisticated devices with enhanced performance, reliability, and functionality. Despite challenges in signal integrity, manufacturing complexity, and thermal management, the benefits of multi-layered PCBs far outweigh the challenges, making them indispensable in a wide range of high-frequency applications, including telecommunications, aerospace, automotive, and medical electronics. With ongoing advancements in materials, fabrication techniques, and design methodologies, multi-layered PCBs are poised to continue driving innovation in high-frequency electronics for years to come.
19.06.2024
and get your PCBA quote within the next 10 minutes!