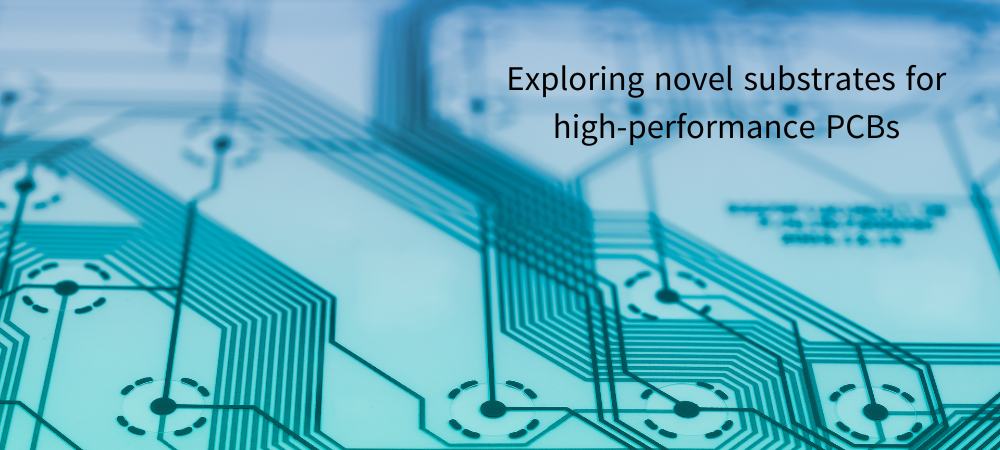
Printed Circuit Boards (PCBs) serve as a fundamental infrastructure for electronic devices, facilitating the connecting of diverse electronic components. The advancement of electronic devices necessitates PCBs that exhibit improved performance, streamlined designs, and expanded capabilities. The study of new substrates for high-performance PCBs is a crucial factor in attaining these objectives. This article explores the progress and potential future developments associated with the utilization of novel materials as substrates for PCBs.
Traditional substrates
FR-4 (Flame Retardant 4) has historically been the standard substrate material for PCBs due to its low cost and relatively excellent performance. Nonetheless, as electronic devices become more complex and compact, the limitations of traditional substrates, such as limited thermal conductivity and poor signal integrity at high frequencies, have become evident.
As a flame-retardant material, FR-4 complies with fire safety standards and is extensively used in applications where fire resistance is a crucial requirement. The dielectric constant of FR-4 is typically between 4.2 and 4.7. This property is crucial because it determines how quickly signals can propagate through a material. Regarding thermal stability, FR-4 performs admirably, withstanding a wide temperature range without substantial degradation. Moreover, FR-4 possesses exceptional mechanical strength and durability. In addition to being an inexpensive and widely available substrate material, it is also favored for a variety of general-purpose applications.
However, FR-4 has the following limitations:
- Relatively low thermal conductivity in comparison to some modern substrates. In high-power applications, this restriction can contribute to heat buildup, potentially affecting the device's performance and dependability.
- Signal Integrity at High Frequencies: FR-4 may be unable to maintain optimal signal integrity at high frequencies, resulting in signal loss and distortion.
- FR-4 is not suitable for malleable or bendable electronic devices due to its lack of flexibility. In applications requiring flexibility, polyimide is frequently substituted for other materials.
Advanced substrates
Polyimide
Polyimide, a versatile and sophisticated substrate material for PCBs, has risen to prominence in the electronics industry as a result of its distinctive set of properties. Polyimide, renowned for its extraordinary thermal stability and flexibility, is a crucial component in a variety of applications.
Polyimide, which is distinguished by its high-temperature resistance, is stable even in severe environments. This characteristic makes it ideal for applications in the aerospace, automotive, and industrial sectors, where electronic components may be exposed to high temperatures.
The flexibility of polyimide is another notable characteristic. Polyimide, unlike traditional rigid substrates, permits the fabrication of malleable and bendable PCBs. This quality is particularly advantageous in applications where space is limited or where conformal designs are required.
Polyimide PCBs are frequently utilized by the aerospace industry due to their light weight and ability to conform to complex geometries. In automotive applications where vibration and thermal stress are prevalent, the flexibility of polyimide ensures the PCBs' durability. Figure 1 shows a flexible PCB with polyimide substrates.
Figure 1: Flexible PCB manufactured with polyimide substrates (Source: Cadence)
In addition to its physical properties, polyimide possesses superb dielectric properties. It maintains consistent electrical performance, making it appropriate for high-frequency applications. In telecommunications and other industries where signal integrity is of the utmost importance, polyimide PCBs are useful for maintaining peak performance.
However, polyimide does have some limitations. While it performs exceptionally well in high-temperature environments, its thermal conductivity is relatively lower compared to other options. In applications with intensive heat production, additional measures may be necessary to effectively manage and dissipate heat.
Moreover, polyimide can be more expensive than conventional substrates such as FR-4. This cost factor may impact the selection of substrate material, especially in mass-produced consumer electronics where cost considerations are crucial.
Rogers Corporation's high-frequency laminates
Rogers Corporation's high-frequency laminates are a significant advancement in the domain of PCB substrates, offering a unique set of characteristics that meet the stringent requirements of high-frequency applications.
Low dielectric constant is one of the distinguishing characteristics of Rogers Corporation's laminates, which contributes to the efficient transmission of signals. This characteristic makes them ideal for applications in which maintaining signal integrity at high frequencies is crucial, such as communication systems, radar systems, and high-frequency circuits.
The low dissipation factor of these laminates enables the fabrication of high-performance PCBs with minimal signal loss. This property is essential for applications where the precision and dependability of transmitted signals are crucial, such as wireless communication devices and advanced radar systems.
The exceptional dimensional stability of Rogers' laminates (Figure 2) ensures that the electrical properties of the material remain constant across a range of temperatures and environmental conditions. This stability is crucial for maintaining the efficacy of high-frequency circuits, particularly in applications with significant temperature variations.
Figure 2: RO4500 laminates (Source: Rogers Corporation)
These high-frequency laminates have found widespread use in the design and production of antennas, satellite communication systems, and high-frequency sensors. Particularly, the telecommunications industry benefits from the superior electrical properties of Rogers Corporation's laminates for optimal data transmission performance.
However, the advanced properties of these high-frequency laminates are frequently accompanied by a higher price tag than conventional substrate materials. This can affect the total cost of the electronic device, thereby influencing mass-produced consumer electronics decisions.
Moreover, the manufacturability of high-frequency laminates may necessitate the use of specialized processes, which can present challenges in terms of scalability and integration with existing manufacturing workflows.
DuPont's Pyralux
Pyralux, a flexible circuit material manufactured by DuPont, stands out as a pioneering substrate for PCBs. Pyralux is characterized by its flexibility, which enables designers to create circuits that conform to unorthodox shapes and designs. This quality is especially advantageous in industries where space limitations and complex form factors are crucial considerations.
Pyralux is typically comprised of a polyimide film, which functions as the flexible base, and copper layers for conducting traces. This composition imparts exceptional thermal stability, ensuring that the material can withstand a range of temperatures without performance degradation. Pyralux is suitable for applications in aerospace, automotive, and medical devices where flexibility and dependability are of the utmost importance due to its robust thermal stability.
The applications of Pyralux include miniaturized and lightweight electronic devices. Its flexibility permits the fabrication of bendable circuits, making it ideal for use in wearable technology, flexible displays, and medical sensors. Particularly, the medical industry benefits from Pyralux's use in the creation of flexible circuits for implants and diagnostic devices.
Despite its numerous benefits, Pyralux is not without disadvantages. This sophisticated material can be more expensive than conventional rigid substrates, which impacts the total cost of the electronic device. In addition, the manufacturing processes for Pyralux may differ from rigid PCBs, necessitating the use of specialized apparatus and knowledge. This can present difficulties in terms of scalability and mass production, especially for industries with high production volume requirements.
Metal Core PCBs
Metal Core PCBs, also known as MCPCBs, take a unique approach to the design of PCBs by incorporating a metal core, typically aluminum or copper. This design decision confers a set of characteristics that make MCPCBs particularly suitable for applications with high power requirements or demanding thermal conditions.
Metal Core PCBs effectively evacuate the heat generated by electronic components due to their enhanced thermal conductivity. The metal interior functions as a heat sink, facilitating the removal of heat from vital components. This thermal management capability is essential in applications such as LED illumination, power supplies, and automotive electronics, where effective heat dissipation is essential for device reliability and longevity.
In addition to contributing to the mechanical robustness of MCPCBs, the metal core provides robust component support. This is particularly advantageous in applications subject to physical stress or vibrations, as is common in automotive and industrial settings.
Metal Core PCBs (Figure 3) have applications in areas with high power densities, such as power converters and motor drives. The thermal efficiency of MCPCBs ensures that electronic components can operate optimally under challenging conditions, thereby reducing the danger of overheating and enhancing the overall performance of the system.
Figure 3: Aluminium-based LED PCB
However, the metallic core can make these boards heavier and potentially more expensive than conventional FR-4 boards, limiting their application in certain consumer electronics where weight and cost are crucial. In addition, the metal core reduces the flexibility of these PCBs in comparison to flexible substrates such as polyimide.
Emerging technologies
Graphene's electrical conductivity and mechanical robustness make it promising for high-performance PCBs. These PCBs use graphene, a hexagonal lattice of carbon atoms, to provide many unique qualities that could revolutionize electrical devices.
Graphene's electrical conductivity makes it excellent for high-performance PCBs. More electron mobility than typical materials makes graphene quicker and more efficient at signal transmission. This characteristic benefits advanced communication systems and data processing units that need fast data transport.
Graphene's high thermal conductivity makes heat dissipation efficient, solving one of electrical device design's biggest problems. In high-power applications, graphene-based PCBs may reduce overheating and improve electronic component reliability and durability.
The two-dimensional structure of graphene layers allows ultra-thin and lightweight PCBs, making them ideal for devices with limited area and weight. This could lead to smaller, lighter electronics. Many industries could benefit from graphene-based PCBs. Graphene's electrical and thermal properties improve electronic systems in aircraft, telecommunications, medical equipment, and consumer electronics.
Graphene-based PCBs confront numerous obstacles to mainstream implementation. High-quality graphene synthesis at scale requires cost-effective manufacturing technologies. Adapting and optimizing graphene into PCB production methods challenges scalability and compatibility with current manufacturing equipment.
Moreover, despite graphene's remarkable mechanical strength, it lacks the flexibility of certain polymer-based materials. This restriction may affect its applicability in devices requiring flexibility or conformability, such as wearable electronics or flexible displays.
Liquid Crystal Polymer (LCP) substrates are adaptable and high-performance PCB materials. Electrical features like low dielectric constant and dissipation factor make LCP famous. LCP substrates are ideal for high-frequency applications that require signal integrity. Telecommunications, aircraft, and high-speed data communication benefit from LCP's dependable signal transmission at high frequencies.
Another benefit of LCP is heat stability. LCP has a high glass transition temperature and maintains its structural and electrical qualities at many temperatures. LCP substrates are ideal for automotive electronics and industrial control systems because to their heat endurance.
LCP's mechanical properties contribute to its widespread use in PCB design. LCP substrates can be manufactured as thin, flexible sheets, enabling the production of flexible and rigid-flex printed circuit boards. This adaptability is especially beneficial in industries such as medical devices and wearable electronics, where conformal and lightweight designs are essential.
LCP substrates are utilized in a wide range of industries. From medical implants and portable electronics to high-frequency communication devices and antennas, LCP's versatility meets the needs of contemporary electronic systems.
However, the cost of manufacturing LCP-based PCBs can be higher compared to traditional materials like FR-4. This cost factor may influence the selection of substrate material, particularly in consumer electronics where cost considerations play a significant role.
3D-printed substrates represent a new frontier in electronics manufacturing, ushering in a paradigm shift in design flexibility and customization. In conjunction with the adaptability of additive manufacturing, the characteristics of 3D-printed substrates enable the creation of electronic devices tailored to specific requirements.
3D-printed substrates are distinguished by their ability to produce intricate and complex designs with relative simplicity. This versatility enables the direct integration of three-dimensional features into the substrate, thereby enabling the construction of compact and custom-shaped electronic components. This capability is especially advantageous in applications where space limitations and unconventional form factors play a significant role.
Numerous industries, including healthcare, aerospace, and robotics, can benefit from 3D-printed substrates. In the medical field, for example, 3D-printed substrates facilitate the creation of implantable medical devices that are tailored to the specific needs of each patient. In aerospace, 3D printing contributes to the construction of highly efficient and space-optimized electronic components due to its lightweight and geometric flexibility.
Rapid prototyping is another domain where the adaptability of 3D-printed substrates is evident. Engineers and designers are able to rapidly iterate and test various PCB designs without requiring extensive tooling modifications. This accelerates the product development cycle and enables more efficient design exploration.
However, 3D printing materials may have distinct electrical and thermal properties than conventional PCB substrates. To achieve the same level of performance and dependability as conventional materials, 3D printing technology and materials science may require continued development.
Moreover, 3D printing's scalability for mass production remains a challenge. While 3D printing is optimal for prototyping and low-volume production, it may not be as efficient or cost-effective for mass production of electronic devices as traditional manufacturing techniques.
Conclusion
The evolution of PCB substrates is a dynamic field propelled by the rising demand for contemporary electronic devices. Exploration of novel substrates is essential to pushing the limits of performance, and as technology develops, the landscape of PCB materials is likely to endure significant changes. Performance, cost, and manufacturability must be balanced in order for these novel substrates to be widely adopted.
07.03.2024
and get your PCBA quote within the next 10 minutes!