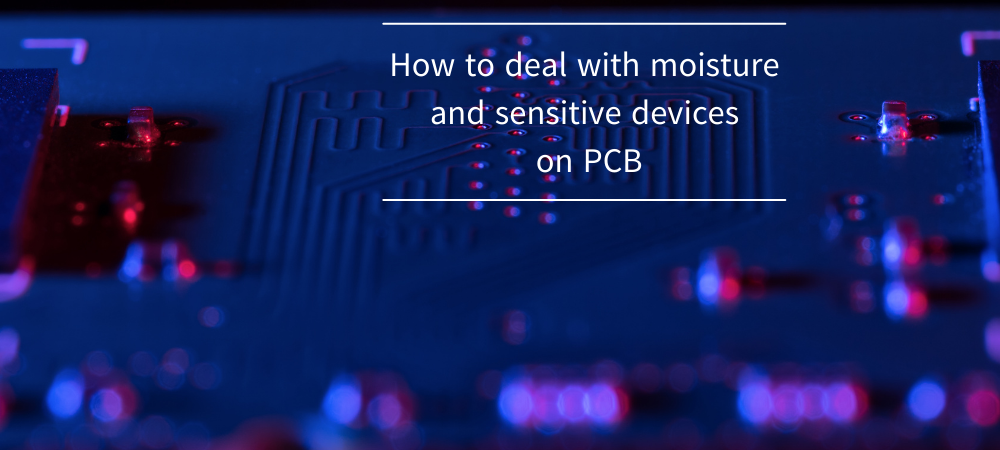
In recent years, electronic devices have undergone a continuous evolution that has led to ever smaller footprint, accompanied by ever higher performance and speed. Smaller, more complex and denser PCBs require appropriate protection of the electronic parts in order to avoid possible corrosion phenomena when exposed to moisture and contaminants. Those agents can in fact degrade the circuit performance, or cause short circuits and failures.
Moisture, for instance, can cause different types of failures on a PCB, depending on which components or conductive traces come into contact with it. The most common issues related to moisture include a lag in the signals transmission, as well as increased propagation delays. Once a certain threshold is exceeded, the circuit may stop working entirely.
Electronic devices can suffer internal damage if not handled and stored by applying industry specific standards. Components with Ball Grid Array (BGA) and chip scale packages are particularly sensitive to moisture, and even worse, damage to these components can be difficult to detect during inspection. Figure 1 shows an example of damage caused to the PCB by moisture.
Figure 1: Damage produced by moisture on the PCB
Sensitive components and MSD
A few drops of water may be enough to irreparably damage a PCB, but an even lower amount of moisture can be harmful. Moisture represents an issue not only during the operation of the circuit, but also during the storage of the boards, before they are installed.
Pure or demineralized water has a resistivity of approximately 1.8 x 107 Ω x m at 25°C, making it a much better insulator than an electricity conductor. Actually, the water with which a PCB can come into contact contains dissolved salts and minerals, chlorides, sulphates and carbonates. The presence of these materials makes water highly conductive, representing a potential threat to the integrity of the printed circuit board, causing short circuits and corrosion processes.
An even worse threat is condensation, which occurs when the PCB surface is colder than its surroundings. Condensation can form both on the external faces of the board and inside the component packages, which must therefore be selected taking this aspect into consideration.
Electronic components that are particularly sensitive to moisture, identified with the acronym MSD (Moisture Sensitive Device), require an appropriate protection both during the PCB assembly process and during the storage phase of the finished boards in the warehouse. When a component has a moisture absorption coefficient that is too high, there is the potential risk of damaging the board, the components, or the electrical connections among them. Excessive moisture during the soldering process can cause damage to the material used for the board substrate. These types of defects are not easily detectable and have a tendency to manifest themselves only on the final product or after a certain time of use, drastically reducing the possibility of remedying them.
The greatest risks occur during the reflow soldering process, when MSD components are placed on the PCB. Even large and sudden variations in ambient temperature can cause expansion or cracking of the package. A very common effect produced by moisture is the internal delamination of the material used to build the PCB. The common FR-4, for example, is a highly hygroscopic material and is therefore particularly sensitive to environmental humidity, regardless of the packaging methods. Any moisture not eliminated during the welding phases turns into steam, causing delamination and microcavities in the most sensitive areas of the board.
IPC standards for sensistive devices
The first standards relating to moisture control in PCB were released in 2010 by the IPC, the organization initially known as Institute for Printed Circuits. By following these standards, electronic boards can last longer, provided proper techniques are used to diffuse moisture. In addition, boards protected by a suitable coating can maintain their solderability for longer periods, provided that measures are taken to prevent moisture from entering them.
According to the same guidelines, baking is a practical method for removing moisture from PCBs if it had not been possible to prevent its entry previously. However, baking in oven inevitably leads to an increase in costs, an extension of production times and a lower solderability. This method should therefore be avoided as much as possible, preferring instead preventive maintenance techniques during assembly and storage of PCBs.
There are currently two ICP-issued standards that can guide electronic manufacturers in handling moisture sensitive components: IPC/JEDEC J-STD-020E and IPC/JEDEC J-STD-033D.
IPC/JEDEC J-STD-020E
This standard offers a classification system for determining the initial reliability qualification. After identification, manufacturers can package, store and handle devices to reduce thermal and mechanical damage during the reflow process.
IPC/JEDEC J-STD-033D
This standard provides an end-user methodology for handling, packaging and shipping MSDs, as well as procedures to increase yield and limit reliability degradation.
Both standards divide moisture sensitivity levels, or MSL, into classes numbered 1 to 6 depending on their susceptibility to moisture-induced damage. The higher levels apply to sensitive components that offer greater resistance to moisture. In particular, for each class, it is indicated how long the component can remain outside a moisture protection system before requiring baking in oven to remove the absorbed moisture.
As you can seen in the table in Figure 2, the MSL 6 level corresponds to the most sensitive components, which need to go through baking even before being used.
Figure 2: The MSL classes (Source: TI)
PCBs, as well as finished boards, should instead be stored and shipped using special protective bags (which generally provides both ESD and moisture protection), known as MBB (Moisture Barrier Bag) bags. An example of such bag is shown in Figure 3.
*
Figure 3: MBB protective bags
How to protect components and PCB
To protect PCBs from moisture, the best approach is to intervene appropriately in all phases of PCB manufacturing, as well as in the subsequent storage or shipping phases.
Manufacturing
During the production of PCBs, the lamination process must be carried out in an environment with controlled temperature and moisture using, if necessary, suitable drying agents. Staff should always wear clean gloves whenever a new production batch is started, thus avoiding contamination between different components. During the PCB lamination process, the different layers that make up the PCB are positioned and glued to form a single board. During this phase, some manufacturers apply a low-pressure vacuum effect, avoiding the formation of gaps that could trap moisture inside them.
Another common technique is to use copper plates with a meshed structure, in order to create stronger bonds and prevent the movement of moisture between the different layers of the PCB. However, it should be noted how these structures can affect the electrical performance of the board and their use must therefore be properly considered.
After PCB fabrication, a surface finish can be applied for protective purposes. In this way, the properties of the PCB are kept intact until the next assembly stage.
Assembly
To prevent ambient moisture from adversely affecting the PCB, soldering of components should be performed at high temperatures with a humidity level below 0.1%, or at low temperatures with a humidity level below 0.2%. High temperature soldering is performed around 260°C, while low temperature soldering occurs around 230°C.
After completing the assembly of the components on the board, cooking in oven is a common and effective practice for removing moisture. However, it is necessary to ensure that the thermal expansion coefficient (CTE) of the material used for the PCB is not exceeded, thus avoiding delamination or cracks.
Arguably, the best form of protection for an assembled PCB consists in applying one among the several available types of conformal coating. Conformal coating protects not only from moisture, but also from fluids, contaminants and even ultraviolet rays.
Conformal coating consists of a thin polymer film applied to the PCB to protect the board and its components from the environment and corrosion. The film typically has a thickness between 25 and 250µm and has the property of adapting to the shape of the board and its components, covering and protecting solder points, terminals and pins of electronic devices, exposed traces and other copper areas from corrosion, thus extending the operating life of the PCB.
Figure 4 shows the corrosive effects produced on the PCB by moisture or other aggressive agents in the case of a board without conformal coating (image on the left) and with conformal coating (image on the right). These coatings form a uniform layer that covers the surfaces of the board, providing excellent repellency to moisture, oils, dirt, fingerprints and other environmental contaminants. Conformal coating provides protection from various corrosive agents such as moisture, water, salt spray, haze and sulfur.
Figure 4: Board with and without conformal coating (Source: 3M)
Encapsulation, which consists of fully inserting an assembled PCB inside a protective enclosure, can also prove to be a very effective method, as long as the enclosure allows trapped moisture to escape to the outside, for example through air vents.
An alternative to full encapsulation consists in the partial coating of the board using appropriate epoxy resins that cover only some areas of the PCB particularly sensitive to humidity.
Storage
Printed circuit boards (assembled or not) should be stored in the appropriate MBB protective bags and not in envelopes that only provide ESD protection.
Designers should also observe the guidelines contained in the IPC standards, which provide valuable recommendations for packaging and storage of electronic devices, minimizing the chance of moisture diffusion.
Failure to apply PCB moisture protection to boards can cause PCB failures and unnecessary costs for repairs or replacements. However, by applying the techniques listed above for manufacturing, assembly, and packaging or storage, it is possible to greatly reduce the possibility of moisture and other similar agents threatening the functioning and reliability of the PCB.
Conclusion
With the current trend towards miniaturization and component density growth, designers face new challenges to provide PCBs with an adequate level of protection from moisture and corrosive agents. Moisture Sensitive Devices, or MSDs, have an increased sensitivity to moisture which can render the devices inoperable. The article has described the main techniques which, applied during the production, assembly, storage and shipping phases of an electronic board, allow to provide valid and lasting protection to the electronic circuit.
20.03.2023
and get your PCBA quote within the next 10 minutes!