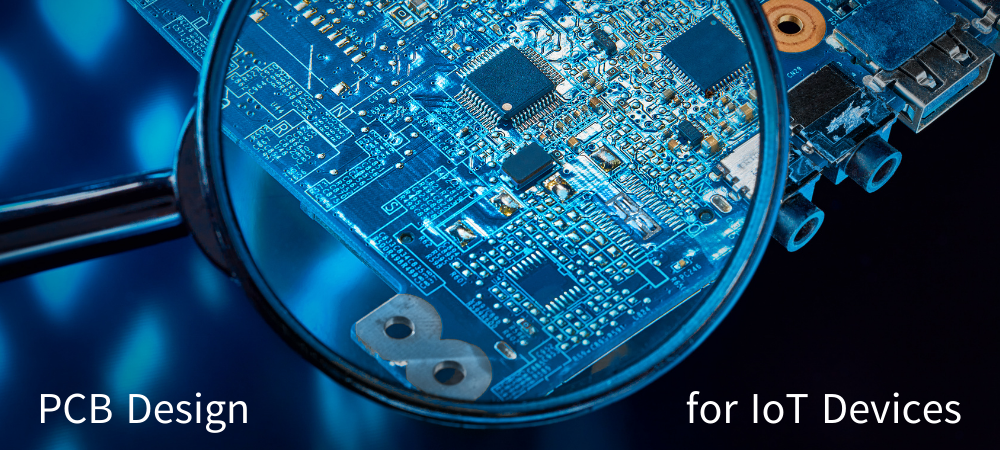
As the Internet of Things (IoT) continues to revolutionize industries such as consumer, healthcare, and agriculture, designing printed circuit boards (PCBs) for IoT devices has become a critical task. These devices often require compact, power-efficient, and high-performance PCBs to meet their specialized functions and environmental demands.
However, achieving these goals is challenging due to constraints like limited space, strict power requirements, wireless communication needs, and rigorous durability standards. This article examines the challenges of PCB design for IoT devices and proposes effective solutions.
Challenges in IoT PCB design
Below is a list of key challenges engineers encounter when designing PCBs for IoT applications.
1. Miniaturization and space constraints
IoT devices are typically compact, with dimensions often dictated by the form factor of wearables, smart sensors, or other embedded systems. This miniaturization (Figure 1) creates limited space for components, traces, and interconnects on the PCB. Designers must balance functionality and size without compromising performance or reliability.
Figure 1: A compact PCB for IoT application (Source: RS)
2. Power efficiency
IoT devices are often battery-powered and expected to operate for extended periods without frequent recharging or replacement. Efficient power management becomes crucial, as poor PCB design can lead to energy loss and reduced battery life. Components like voltage regulators, low-dropout regulators (LDOs), and power management ICs (PMICs) must be carefully selected and integrated.
3. Wireless connectivity
Most IoT devices rely on wireless communication technologies such as Wi-Fi, Bluetooth, Zigbee, or LoRa. These technologies require well-designed antennas, proper impedance matching, and minimal signal interference. PCB designers face the challenge of ensuring strong signal integrity while fitting antennas and RF components into a compact layout.
4. Thermal management
The compact design of IoT devices can lead to heat concentration, especially in high-performance applications like edge AI or video streaming. Poor thermal management can degrade device reliability and shorten the lifespan of components.
5. Signal integrity and electromagnetic interference (EMI)
IoT devices often operate in environments with significant electromagnetic noise. Ensuring signal integrity and reducing EMI are critical to maintaining reliable performance. This becomes particularly challenging as PCBs become more compact, increasing the risk of crosstalk and signal degradation.
6. Durability and environmental considerations
IoT devices may be deployed in harsh environments, exposed to factors like moisture, dust, and extreme temperatures. PCBs must meet stringent durability standards, including conformal coating and robust materials.
Solutions for Compact, Efficient IoT PCB Design
Multilayer PCBs
To address space constraints in IoT devices, designers often use multilayer PCBs. By adding multiple layers, they can segregate power and signal traces, integrate ground planes for electromagnetic interference (EMI) shielding, and accommodate more components in a compact space.
This approach helps achieve high-density designs without compromising performance. Furthermore, advanced PCB stack-ups (Figure 2) allow for better thermal management and enhanced signal integrity by isolating sensitive traces from power or high-frequency paths. Modern multilayer designs also facilitate the integration of mixed signal and RF circuits on the same board, ensuring more efficient and seamless operation of IoT systems.
Figure 2: Stackup of a multilayer PCB (Source: elecrow)
Advanced power management
Energy efficiency is a critical consideration in IoT PCB design, as many devices operate on battery power. Designers can significantly improve energy consumption by incorporating ultra-low-power components and optimizing power delivery networks (PDNs). Techniques such as dynamic voltage scaling (DVS) allow the voltage supplied to components to vary based on workload demands, reducing power draw during low activity.
Sleep mode circuits and power gating also help conserve energy during idle times. Additionally, selecting integrated power management ICs (PMICs) with features such as voltage regulation, power sequencing, and energy monitoring not only simplifies the design but also saves valuable board space and reduces component count. These strategies contribute to extending battery life and reducing the need for frequent recharges or larger power sources.
Optimized antenna placement and RF design
Wireless communication is at the heart of IoT devices, and antenna design and placement are essential for ensuring robust performance. Designers must carefully plan antenna orientation and positioning to avoid interference and ensure optimal signal strength. Techniques such as coplanar waveguides, impedance matching networks, and dedicated RF shields help improve signal quality and minimize losses.
Proper grounding and decoupling are also essential to prevent noise and signal degradation. Simulation tools are invaluable in this phase, allowing designers to model the antenna performance and predict potential interference or mismatch issues before physical prototypes are created. Accurate RF simulations, including those for signal reflection and antenna radiation patterns, help optimize the final design for better connectivity and range.
Figure 3: A compact embedded board provided with a PCB-integrated antenna (Source: Techplayon)
Efficient thermal management
As IoT devices become smaller and more powerful, managing heat dissipation is increasingly important. Heat buildup can affect both the performance and lifespan of components. Designers incorporate heat dissipation techniques such as thermal vias, heat sinks, and copper pours to effectively manage temperature.
Thermal vias, for example, allow heat to be transferred between layers to dissipate heat away from sensitive areas. Heat sinks and copper pours spread the heat over a larger area, promoting even heat distribution. Additionally, incorporating low-power components reduces overall heat generation. Thermal simulation software enables designers to predict hotspots and optimize the layout for uniform heat dissipation. This ensures that temperature-sensitive components, such as microcontrollers or RF transceivers, remain within safe operating ranges.
Grounding and shielding
Proper grounding and shielding practices are critical for reducing EMI and ensuring signal integrity in compact IoT devices. Ground planes on multilayer PCBs play a key role in stabilizing signals and preventing ground loops, which can cause noise and performance degradation.
Effective EMI shielding, whether in the form of metal enclosures or dedicated shielding layers, protects sensitive components from external interference and minimizes radiation from internal sources. In high-speed or RF circuits, differential signaling techniques can help reduce susceptibility to noise, ensuring clean data transmission. Ensuring that the grounding system is robust and consistent throughout the design helps maintain both functional and electromagnetic compliance.
Robust material selection
The choice of materials is critical in IoT PCB design to ensure durability, reliability, and optimal performance in varying environments. Using high-quality, durable materials ensures that the PCB can withstand mechanical stresses, temperature fluctuations, and exposure to elements such as moisture and dust. Flexible PCBs, made from materials like polyimide, are often used in wearable devices or devices that need to conform to non-flat surfaces.
These flexible boards reduce bulk while providing high-density functionality. Conformal coatings, often applied to the surface of the PCB, offer additional protection against environmental contaminants and corrosion, enhancing the device's longevity. Furthermore, selecting materials with low loss tangent and high thermal conductivity can optimize signal integrity and heat management.
Design automation and simulation tools
Modern PCB design tools are indispensable for compact IoT designs, offering advanced features that enable efficient design and rapid prototyping. Tools such as Altium Designer, KiCad, or Cadence Allegro provide designers with comprehensive solutions that support simulation, rule-checking, and 3D visualization. These capabilities help identify potential issues early in the design process, such as signal integrity problems, power distribution bottlenecks, or thermal hotspots.
Signal and power integrity simulations are especially important for complex IoT boards, where multiple high-speed signals and power rails are interacting. With integrated simulation tools, designers can perform tests like time-domain reflection (TDR) analysis, cross-talk analysis, and voltage drop analysis, ensuring that the final design is both high-performing and reliable. Moreover, automated rule-checking features help ensure that the design adheres to industry standards, reducing errors and the need for costly reworks.
Best practices for IoT PCB design
Component placement - Arrange components logically to minimize trace lengths and avoid crossing signals. Place high-speed components and RF modules away from noisy power circuits.
Trace routing - Use wide traces for power lines to reduce resistance and maintain signal quality. Avoid sharp bends in traces to minimize signal reflection.
Layer Stack-Up - Dedicate separate layers for power, ground, and signals in multilayer PCBs. A well-planned stack-up improves EMI performance and simplifies routing.
Testing and Validation - Rigorously test PCBs for signal integrity, thermal performance, and EMI compliance. Prototyping and iterative design cycles ensure a reliable final product.
Future trends in IoT PCB design
The evolution of IoT technology continues to influence PCB design. Flexible and stretchable PCBs are gaining traction, enabling innovative applications in healthcare and wearables. Advances in semiconductor technology, such as system-on-chip (SoC) and system-in-package (SiP) solutions, further integrate functionality into compact designs. Additionally, the adoption of artificial intelligence (AI) in design automation is expected to streamline the process of creating efficient IoT PCBs.
Conclusion
Designing PCBs for IoT devices requires a delicate balance of miniaturization, power efficiency, wireless communication, and durability. By leveraging modern techniques such as multilayer designs, advanced power management, and robust materials, engineers can create compact and efficient boards that meet the demands of IoT applications. As technology advances, new tools and materials will continue to enhance the capabilities of IoT devices, driving innovation across industries.
11.02.2025
and get your PCBA quote within the next 10 minutes!