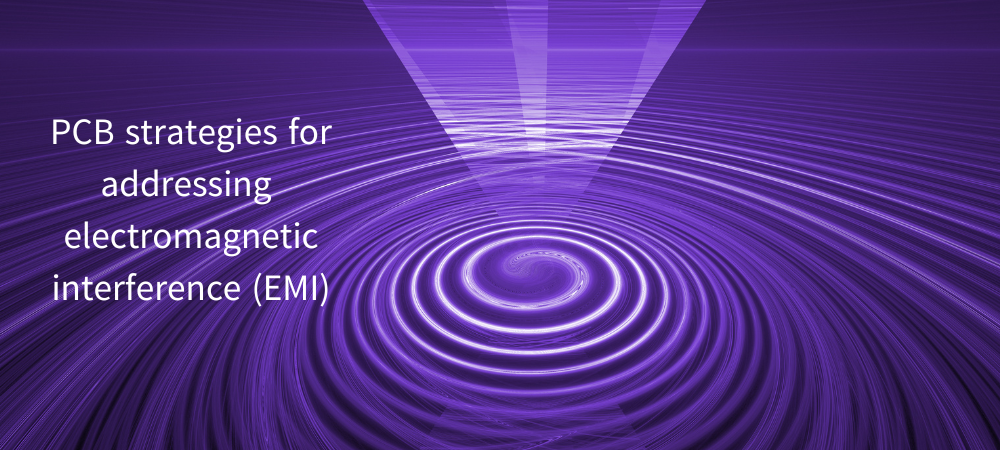
Managing electromagnetic interference (EMI) is one of the major challenges electronic designers must face to ensure that printed circuit boards (PCBs) can operate correctly and reliably. EMI refers to the unwanted electromagnetic energy that interferes with the normal operation of electronic devices, potentially causing malfunction or failure.
EMI mitigation becomes more relevant as electronic components are densely packed, operate at higher frequencies, and must adhere to stricter tolerances. Layout techniques, grounding procedures, shielding, filtering, and component placement are some of the EMI mitigation strategies discussed in this article.
PCB layout techniques
Controlling EMI is heavily dependent on the PCB layout. Designers can reduce the risks of electromagnetic interference problems by using proper layout strategies, such as those outlined below.
Signal routing
Signal routing is a key factor to consider in PCB design. It is important to route high-speed signals carefully to limit the length of traces, as longer lines can operate as antennas and emit electromagnetic interference.
Designers should use differential pairs when routing high-frequency signals as they can effectively eliminate common-mode noise. In addition, minimizing the length and ensuring a direct path for signal traces decreases the likelihood of them functioning as radiation emitters. It is essential to avoid right-angle bends since they can lead to reflections and amplify EMI. Instead, it is advisable to use 45-degree angles or curved traces (Figure 1).
Figure 1: Traces with 90° angles shall be avoided
Layer stackup
The arrangement of layers of a PCB has a considerable impact on its EMI performance. A properly designed layer stackup can offer efficient shielding and aid in impedance control. An instance of this is when a continuous ground plane is positioned adjacent to a signal layer, resulting in the formation of a return path with low inductance. This, in turn, decreases the likelihood of electromagnetic interference (EMI).
A common stackup configuration may consist of alternating layers of signal and ground or power planes, with high-speed signal layers positioned next to ground planes. This design effectively mitigates electromagnetic interference and minimizes signal interference between different channels.
Return paths
It is crucial to ensure that signal traces have a distinct and low-inductance return channel to minimize EMI. Signal traces shall be accompanied by a nearby ground plane to enable the return current to pass directly beneath the signal trace. This close distance decreases the size of the loop, which is an important aspect in reducing the electromagnetic waves emitted.
When the return path is disrupted, it might cause the current to follow a longer and less direct course, resulting in an increase in loop area and EMI.
Grounding techniques
Grounding is an essential element of PCB design, particularly when dealing with EMI. An effectively engineered grounding system can inhibit the propagation of noise and minimize vulnerability to external interference.
Ground planes
Using a solid ground plane is a highly effective method for managing EMI. Ground planes serve as pathways with low impedance for return currents and offer protection to delicate circuits by shielding them from radiated noise. Multiple ground planes in multilayer PCBs can provide additional shielding and effectively decrease EMI. Ground planes need to remain solid and without any breaks or divisions, as interruptions can lead to pathways with high impedance and result in increased noise.
Grounding schemes
There are different grounding schemes that designers can use, depending on the application. A common approach is to use a single-point ground, where all ground connections converge at a single location. This method is effective for low-frequency designs. For high-frequency designs, a multipoint ground may be more appropriate, where ground connections are made at multiple locations to minimize inductive loops. Additionally, the separation of analog and digital grounds can prevent noise from digital circuits from contaminating sensitive analog signals. If separation is necessary, the grounds should be connected at a single point, typically near the power source.
Ground loops
Ground loops are a significant source of EMI. These occurrences arise from the existence of many ground paths that create a loop, leading to the reception of interference and the introduction of noise into the system. To avoid ground loops, designers must establish a singular point for all ground connections and avoid creating several channels that could potentially create a loop. By implementing a star grounding system, where all ground connections originate from a central point, ground loops can be efficiently avoided.
Shielding
Shielding is an effective method for containing and controlling electromagnetic emissions, especially in environments with high levels of EMI or sensitive components.
Shielding can be achieved by using conductive enclosures or casing around the PCB or specific components (Figure 2). These enclosures act as Faraday cages, preventing EMI from entering or leaving the enclosed area. Metallic cases or covers can be used to shield the entire PCB or critical sections. For example, placing a metallic shield over sensitive analog components can protect them from digital noise.
Figure 2: Shields protect sensitive areas of the PCB from EMI
It is crucial to connect shields to the ground to ensure their effectiveness. A shield that is not properly grounded can act as an antenna and exacerbate EMI issues. The ground connection should be as short and direct as possible to provide a low-impedance path. In some cases, grounding the shield at multiple points may be necessary to ensure effective EMI containment.
In addition to external enclosures, PCB-level shielding can be implemented. This involves placing shielding cans over specific components or areas of the PCB. These shields can be soldered directly onto the PCB and are particularly useful in compact designs where space for external shielding is limited.
Filtering
Filters are crucial for preventing unwanted frequencies from propagating through the PCB and causing interference.
Decoupling capacitors (Figure 3) are commonly used to filter out high-frequency noise from power supplies. By placing these capacitors close to the power pins on integrated circuits (ICs), designers can effectively shunt high-frequency noise to the ground, preventing it from spreading across the PCB. It is important to select capacitors with appropriate values for the frequencies of interest and to place them as close as possible to the ICs they are intended to filter.
Figure 3: Decoupling capacitors shall be placed close to the IC’s power pins
Ferrite beads serve as another effective filtering component, providing high impedance at high frequencies and thereby attenuating EMI. These beads are often placed on power lines or signal lines to block high-frequency noise while allowing low-frequency signals to pass through. When selecting ferrite beads, it is essential to consider their impedance versus frequency characteristics to ensure effective filtering at the desired frequencies.
Designers can also implement RC (Resistor-Capacitor) and LC (Inductor-Capacitor) filters to target and attenuate specific frequency ranges. These filters can be used on signal lines to eliminate high-frequency noise or on power lines to provide additional filtering beyond what decoupling capacitors offer. Careful selection of component values is critical to ensure that the filter effectively targets unwanted frequencies without adversely affecting the desired signals.
Component placement
The placement of components on a PCB is a critical factor in controlling EMI. Strategic placement can significantly reduce the potential for interference and enhance the overall performance of the circuit.
Separation of high and low-speed components
It is important to keep high-speed components and traces separate from low-speed and sensitive analog components. High-speed digital signals can generate considerable noise, which can easily couple into nearby analog circuits if not properly isolated. By grouping high-speed components and placing them away from sensitive analog circuits, the risk of interference can be minimized.
Power supply placement
The placement of power supply components, such as regulators, inductors, and capacitors, is also crucial for EMI control. These components can generate significant electromagnetic noise, particularly in switching power supplies. To contain this noise, power supply components should be placed near the power input and away from sensitive areas of the PCB. Additionally, placing decoupling capacitors close to the power pins of ICs can prevent noise from the power supply from affecting the rest of the circuit.
Clock signal management
Clock signals are a common source of EMI due to their high frequency and repetitive nature. Therefore, careful placement of clock generators and routing of clock signals is essential. Clock signals should be kept as short as possible and routed away from sensitive analog circuits. In some cases, using shielding or placing ground traces adjacent to clock traces can help contain radiated emissions.
Design for Manufacturability (DFM)
While the primary focus in EMI mitigation is on design techniques, it is equally important to consider manufacturability to ensure that the design can be effectively produced without compromising EMI performance.
Manufacturing processes inherently involve variability, which can influence the EMI performance of the final product. To account for these variations, designers should incorporate appropriate tolerances into the design. For instance, the placement of components, trace widths, and layer stackup dimensions should all be designed with manufacturing tolerances in mind. This ensures that EMI performance remains consistent across different production batches.
The choice of PCB materials plays a significant role in EMI performance. Materials with high dielectric constants can help reduce the propagation of high-frequency signals, while those with low-loss tangents can minimize signal attenuation. It is crucial to select materials that strike a balance between performance and manufacturability, ensuring that the PCB meets EMI requirements without introducing manufacturing challenges.
The assembly process can also have an impact on EMI performance. For example, solder joints with high inductance can introduce noise into the circuit. To maintain the effectiveness of the EMI mitigation strategies implemented during the design phase, it is essential that assembly processes are tightly controlled, and that components are properly soldered.
Testing and validation
After implementing EMI mitigation strategies, it is crucial to conduct thorough testing and validation to ensure that the PCB meets the required EMI standards.
One of the essential steps in this process is conducting EMI testing in a controlled environment, such as an anechoic chamber. This environment allows designers to accurately measure the electromagnetic emissions from the PCB and identify any potential issues. The testing should encompass both radiated and conducted emissions, ensuring that the PCB complies with all aspects of EMI standards.
EMI testing often uncovers issues that necessitate iterative design adjustments. Based on the test results, designers may need to revisit various aspects of the PCB design, such as layout, grounding, and shielding strategies. This process of iterative testing and refinement is crucial for achieving optimal EMI performance and ensuring that the PCB meets all requirements.
07.12.2024
and get your PCBA quote within the next 10 minutes!