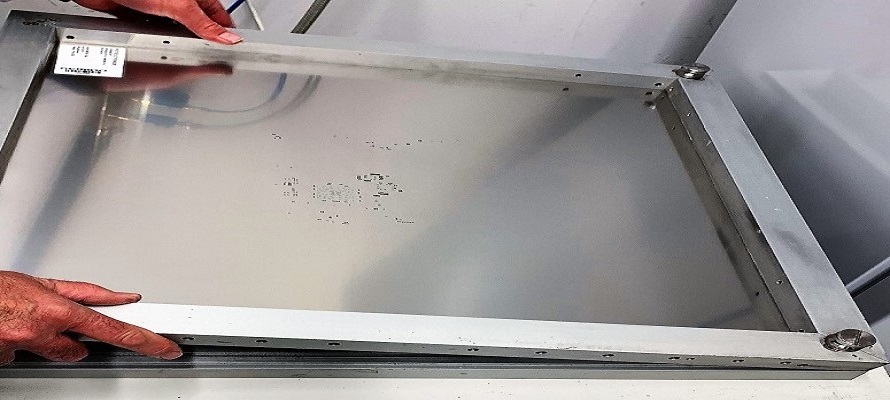
Silkscreen printing – also known as screen printing or serigraphy – is the flagship solution for electronic boards to be fitted with SMD*. This technology is regularly adapted to meet the always evolving requirements for soldering quality and circuit compactness. This is an overview of the current main trends.
Screen printing principles. You create a “stencil”, a metal sheet from which the location of the fitting areas – the conductive area of the printed circuit – have been cut out. You then place this stencil on the electronic board and apply soldering paste by scraping it over the stencil.
Even though this seems easy on paper, silk screen printing for PCB SMD does have some complexity to it: for a quality result, you must be sure to have applied the correct quantity of soldering paste everywhere on the circuit. The transfer quality depends on the speed of the operation, the quality of the stencil, the pitch of the scraper and the adhesive properties of the selected soldering paste. Stencil removal is a critical step.
Another disadvantage: producing the stencil is costly due to the price of some of the materials used, the use of a precision laser for cutting and, finally, the performance of the mechanical system that supports the stencil.
PCB stencil: from drawings to cutting
The American IPC 7525B standard is the reference for stencil production, but it can be adapted to meet specific assembler requirements. The assembler provides files that the manufacturer will use to cut sheet metal of which the thickness can vary from 50 to 300 microns. This step requires a laser cutting machine, an investment that is too high (several hundred thousand euros) for an assembler, even if they are a big stencil user, which explains the specialisation of some players in stencil production.
Which material for the stencil?
In 80% of cases, stencils are made from 127 micron thick stainless steel sheets, a solution adapted to medium complexity boards. But the trend is to create electronic boards with increasingly thin spacing, meaning that the areas to be fitted with components are increasingly small and closer together.
To cater to these new needs, manufacturers must use increasingly thin sheets of materials that are more elaborate than stainless steel. Producing thin spacing (less than 0.5 mm) requires using DATUM FG (fine grain), which is a mixture of nickel and stainless steel of which the properties make stencil removal easier. For even thinner spacing, the stencil is cut from Nickel sheets. Even though it is much harder to work with, this material has high stencil removal properties. The disadvantage of these materials is their cost: a Nickel stencil costs about twice the price of a stainless steel one.
A new material has recently come onto the market: LT123** is somewhere between FG and Nickel. Used on a thin aluminium frame and stretched over a polyester sheet, an LT123 stencil can be used to produce several thousand boards and is an alternative to nickel. Available amongst others in 80 to 10 micron thicknesses, LT123 is exceptionally level and has adherence reduction properties that make it possible to produce very high density stencils. Its fine grain results in an excellent release from the soldering paste. LT123 has been tested and adopted by several assemblers. It is also recommended for 80 and 100 micron thick stencils, as it is stronger than the stencils for self-stretching frames.
and get your PCBA quote within the next 10 minutes!
Taking the choice of soldering paste into account
There are different types of soldering paste, with or without lead. Soldering pastes containing lead are rarely used these days, except for some specific applications, military boards for example. Reserved for the assemblers, the choice of soldering paste has consequences on the manufacturer’s preparatory work which may lead to the width of certain areas being corrected on the stencil.
Independently of the constraints linked to the required paste type, manufacturers may also be brought to modify rectangular or square areas for example, to generate octagons or rounded corners for customers.
Excess thickness and engraving
This flexibility can also be seen in the capacity to locally apply excess thickness to create a multi-level stencil.
Some components require more soldering paste than others. When they need to cohabit on the same board surface, manufacturers have two options:
– either they use a sheet of which the thickness matches the minimum quantity of soldering paste and then bond or solder a second sheet in certain locations to locally increase the paste deposit, with the laser cutting applied to both sheets;
– or they use a sheet of a thickness matching the maximum quantity of soldering paste and locally reduce the sheet thickness by an engraving or planing process.
What support for the stencil?
Industrials who order large series of boards (the automotive sector for example) go for stencils bonded to aluminium frames: a nylon or metal fabric is stretched and bonded to an aluminium frame, the stencil is then bonded to the fabric which will have been previously cut. Such stencils cost slightly over twice the price of a stencil for a self-stretching frame and they take up more storage space.
This high costs encourages prototype assemblers (up to 1 thousand boards) to use stencils mounted on self-stretching frames. This type of frame is placed in the silkscreen printing machine in which an operator places the stencil. Fitting the stencil into some self-stretching frames involves a high risk of being cut for the operator: 127 microns is about the same thickness as a razor blade!
In order to reduce the risk of injuries, ASM DEK has developed Vector Guard, a stencil for self-stretching frames fitted with metal protection around the stainless steel sheet. It is relatively light and therefore easy to fit.
The only issue is the price: a licence has to be purchased to be able to produce Vector Guard frames and the blank stencils are sold at a very high price.
There are currently many solutions to allow screen printing to meet the requirements of safe and quality production. The impact of stencil prices can be significant!
* SMD: Surface mounted devices
** LT123 is the name given to this material by Laser Technology
Our thanks to Alain MILARD, the chief editor of Electronique MAG and director of Laser Technologie France for his contribution to this article.