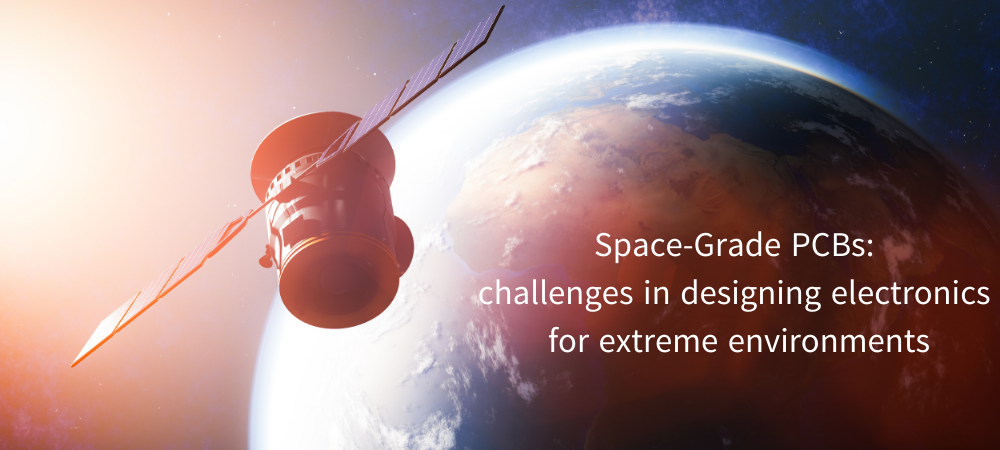
The design and manufacturing of electronic devices capable of withstanding the severe conditions of space have assumed critical importance in the pursuit of cosmic exploration. Printed circuit boards (PCBs) designed for space missions are of the utmost importance in guaranteeing the reliability and functionality of electronic systems. The PCBs are subject to mechanical stresses, radiation, vacuum, and extreme temperatures, which presents engineers and designers with unique challenges. This article explores the intricacies of space-grade printed circuit board (PCB) design and the solutions implemented by engineers to surmount these barriers.
What are the challenges of space-grade PCBs?
To endure the severe environmental conditions of space, space-grade PCBs are specifically designed to function without exception in environments saturated with radiation, high-vibration conditions, and extreme temperatures. Precisely crafted with state-of-the-art materials and manufacturing techniques, these PCBs guarantee outstanding performance and dependability.
Extreme temperatures
Space is characterized by significant variations in temperature. Satellites, probes, and rovers traverse various regions of space while being subjected to extreme temperatures and pressures. Temperatures can range from -200°C in the shadow of a celestial body to over 200°C when exposed to direct sunlight. Sophisticated thermal management techniques and specialized materials possessing low coefficients of thermal expansion are required to accomplish this.
When confronted with extreme temperatures, engineers frequently employ ceramic printed circuit boards (PCBs). Ceramic materials are more resistant to temperature fluctuations due to their low coefficient of thermal expansion. Stability and dependability are exhibited by these materials amidst the extreme temperature fluctuations that are encountered in outer space.
Ionizing radiation
Ionizing radiation emanating from celestial sources and the sun permeates space, presenting a substantial peril to electronic components. Radiation can disrupt the functionality of PCBs and degrade the performance of semiconductors. To protect sensitive electronic components from the damaging effects of radiation, space-grade PCBs must be designed by engineers utilizing radiation-hardened materials, including ceramic substrates and specialized coatings.
Mechanical stresses
During spacecraft launch and deployment, PCBs are subjected to extreme mechanical stresses. Structural damage may result from the vibrations generated throughout the launch phase and the deployment of solar arrays and other components. In order to mitigate this difficulty, designers incorporate shock-absorbing mechanisms, including flexible PCB materials and conformal coatings, to safeguard the electronic components' integrity.
Frequently composed of polyimide, flexible PCBs are more effective at absorbing vibrations and disturbances than their rigid counterparts. Conformal coatings insulate the printed circuit board (PCB) from physical harm throughout the processes of launch and deployment. In addition, meticulous PCB layout design is required to equitably distribute mechanical stresses.
Outgassing
Created during manufacturing, outgassing is a wave soldering defect in which air becomes trapped within a PCB. The air creates cavities or blowholes that have the potential to impair the PCB's performance. This phenomenon occurs both during the wave/hand soldering procedure and when the circuit board is subjected to a high vacuum setting. PCB outgassing is frequently the result of improper material selection and defective manufacturing. Since space is a near-perfect vacuum, devoid of air or any other medium, a defect like outgassing (Figure 1) can potentially contaminate sensitive optical components, like cameras.
Figure 1: Outgassing created in the solder joints after manual soldering (Source: YouTube)
Materials utilized in the fabrication of vacuum-compatible PCBs have minimal outgassing properties. Composites such as polyimide and PTFE (Teflon) are frequently employed owing to their exceptionally low outgassing properties. These materials aid in the prevention of contamination in the vacuum of space and contribute to the electronic systems' long-term dependability.
Space and weight constraints
Due to the strict weight and size restrictions on spacecraft, the creation of electronic systems that are both compact and lightweight has become imperative. A delicate equilibrium must be maintained between size and functionality when designing space-grade PCBs; the architecture must be optimized to maximize the use of available space. By utilizing multi-layer printed circuit boards (PCBs), advanced miniaturization techniques, and three-dimensional packaging solutions, engineers are able to maintain the required performance despite these difficult constraints.
SMT and other advanced miniaturization techniques facilitate the fabrication of electronic components that are both more compact and lightweight. By addressing the challenge of limited physical dimensions, three-dimensional packaging solutions, such as System-in-Package (SiP) or chip-on-board (COB), enable the integration of multiple functions into a compact space.
Substrates for space PCBs
Specialized substrates capable of withstanding the harsh conditions of outer space are required for space-grade PCBs. The substrates most frequently employed are listed below.
Ceramics
Materials such as Alumina (Al2O3) and Aluminum Nitride (AlN) are commonly used ceramics. The low thermal expansion coefficients of ceramics render them exceptionally stable in the face of extreme temperatures. In addition, they are thermally conductive, which aids in heat dissipation. Ceramic substrates offer a resilient solution for space applications due to their intrinsic resistance to radiation.
Glass ceramics
Glass ceramic materials, including Low-Temperature Co-Fired Ceramics (LTCC), are distinguished by their superior electrical properties, minimal thermal expansion, and high thermal conductivity. LTCC is particularly well-suited for applications that necessitate the integration of numerous components into a solitary package and miniaturization.
Polyimide
Polyimide is a flexible and lightweight polymer. Polyimide substrates are well-suited for flexible PCBs, which can absorb mechanical stresses during launch and deployment. They also have good thermal stability, allowing them to withstand temperature variations. However, polyimide may not be suitable for applications with high radiation exposure.
Rad-hard materials
To mitigate the effect of radiation, that can cause electronic components to malfunction or degenerate over time, radiation-resistant materials are incorporated into space-grade PCBs. An example of such a substance is radiation-hardened epoxy laminate. A laminate of this nature has been specially formulated to resist the damaging impacts of ionizing radiation. Its electrical and mechanical properties are intentionally preserved, even when exposed to radiation. The increased resistance of radiation-hardened epoxy laminates to radiation-induced degradation ensures the durability and dependability of space-grade PCBs.
Additionally, copper alloys that possess exceptional resistance to radiation are utilized in space-grade printed circuit boards. Alloys such as copper-tungsten (CuW) and copper-molybdenum (CuMo) provide enhanced durability against degradation and embrittlement caused by radiation. They aid in the preservation of the electrical performance and structural integrity of PCBs in environments with high levels of radiation.
Copper foils
Copper foils are vital to the functionality of space-grade PCBs. Conductive layers are implemented in order to facilitate the transmission of electrical signals. High-performance copper foils are utilized in space-grade printed circuit boards (PCBs) to assure optimal signal integrity and reduce signal loss.
High-performance copper foils are distinguished by a number of essential qualities. Their elevated thermal conductivity facilitates effective dissipation of heat away from the PCB. In space applications, where components generate substantial radiation, this is of the utmost importance. In addition to having a low insertion loss, these foils reduce signal distortion and attenuation. This guarantees consistent signal transmission, even in applications involving high frequencies.
Metal Core PCBs
PCBs with a metal core, comprising a copper or aluminum core surrounded by a dielectric layer, are well-suited for applications that require efficient heat dissipation due to their high thermal conductivity. This is crucial in the space environment, where temperature control is difficult.
Rogers RO4000 series
A family of high-frequency laminates, including RO4350B and RO4003C, Rogers' materials are specifically engineered for use in microwave and RF environments. At high frequencies, the Rogers RO4000 series provides exceptional electrical efficacy. Frequently, these substrates are utilized in space missions that demand RF and microwave capabilities.
PTFE (Teflon)
Polytetrafluoroethylene (PTFE) is widely recognized under the trade designation Teflon. Due to its low loss tangent and dielectric constant, this material is appropriate for high-frequency applications. Moreover, its exceptional resistance to chemicals and minimal outgassing characteristics render it well-suited for utilization in vacuum environments such as space.
High-Tg FR-4
Although FR-4, a prevalent epoxy-based substrate reinforced with glass fibers, finds extensive application in commercial printed circuit boards (PCBs), high-Tg (glass transition temperature) FR-4 variants are engineered to endure elevated temperatures. Compared to conventional FR-4, they exhibit greater stability in the face of extreme temperatures, rendering them viable for specific space applications.
Surface finish
Selected with care, space-grade PCB surface finishes provide oxidation resistance and guarantee dependable solder junctions. Frequently employed are immersion silver and immersion gold finishes (Figure 2).
A silver coating achieved through immersion offers superior conductivity and resistance to corrosion. By establishing a barrier on the copper traces, it effectively safeguards against oxidation and guarantees dependable electrical connections. Silver in immersion is ideally suited for high-frequency applications due to its excellent signal integrity and minimal insertion loss.
In contrast, immersion gold finish furnishes a surface that is exceptionally dependable and long-lasting for solder connections. The oxidation resistance of gold guarantees its exceptional solderability and long-lasting stability. In addition to its high electrical conductivity, immersion gold finish is frequently employed in applications that demand connections with exceptional dependability.
Figure 2: A PCB treated with immersion gold finish (Source: Linkedin)
Conclusion
Complex and arduous, the design of space-grade PCBs necessitates an in-depth comprehension of the extremely harsh conditions that exist in space. Temperature extremes, radiation exposure, vacuum conditions, mechanical stresses, and stringent size and weight restrictions are all obstacles that engineers must overcome. Through the implementation of cutting-edge materials, effective thermal management strategies, radiation-resistant components, and scrupulous design methodologies, engineers are able to fabricate electronic systems that possess the ability to endure the demanding conditions inherent in space exploration.
11.01.2024
and get your PCBA quote within the next 10 minutes!