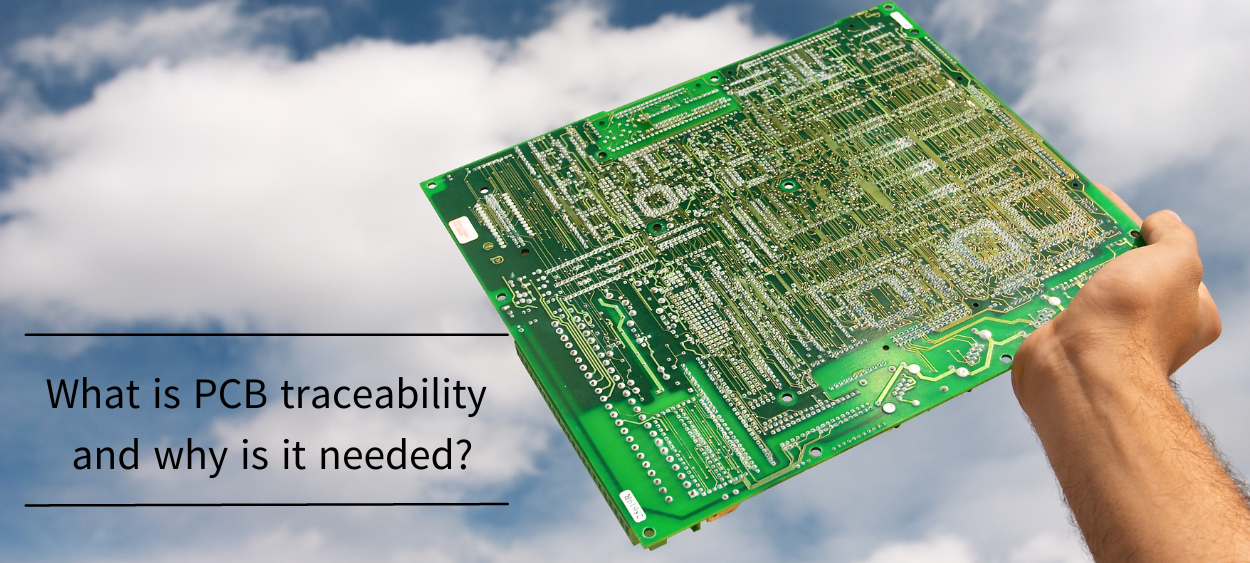
Printed circuit boards (PCBs) are crucial in today's technologically advanced, highly connected society. Many products, from TV remotes to cellphones, are only functional because of the conductive pathways supplied by PCB. A correctly constructed printed circuit board, however, will do more than just supply electricity to an electronic device; it will also give the producer of that device vital information regarding the PCB itself.
The various phases which the PCB undergoes before arriving at the final electronic circuit (drilling, soldering, assembly of components, application of surface finishes, and more) are particularly critical and often conducted in difficult environmental conditions, such as high temperatures, or the presence of fluxes of aggressive substances or acidic cleaners. It, therefore, becomes important for PCB and electronic board manufacturers to ensure long-term traceability of the PCB, both during the various stages of production and in the after-sales market.
Effective marking, which ensures long-term readability through suitable PCB labels, helps electronic equipment manufacturers keep track of PCBs during production, storage, and installation. PCB labels convey critical information in an easily accessible format, including PCB origin, manufacturing lot number, date of manufacture, solder temperature, flux density, and more.
PCB traceability is essential for streamlining production procedures. Yet, as technology develops and boards get smaller and more complicated to build, it becomes more and more challenging.
Data used for traceability
The traceability data associated with a PCB can include different types of information and be available in different forms. For instance, PCB designers might utilize an adhesive label (pre-printed or prepared directly on the assembly line) that includes the following information:
- Serial number
- Production lot
- Date of production
- Name and location of the manufacturer
- Part-specific identifiers
- Data on circuit identification
Given the significance of this data, PCB manufacturers must take specific safety measures to guarantee that all printed codes and markings stay readable for the duration of the circuit board's life.
The traceability of PCBs is crucial for several reasons. It enables producers to pinpoint the origin of any flaws or issues that can appear during manufacturing, enhancing quality control and guaranteeing adherence to rules and regulations. Also, it simplifies maintenance and repairs because personnel can find the root of problems and replace broken parts more rapidly.
Additionally, manufacturers can evaluate the performance of their PCBs over time and pinpoint areas for improvement thanks to PCB traceability, which can aid in product development. Proving that the producer has taken all essential precautions to assure the safety and dependability of their products can also help with liability protection. PCB traceability is a crucial component of PCB production and is becoming increasingly relevant in numerous industries.
Figure 1 shows an example of a PCB label which includes various relevant information for the traceability of the printed circuit board. Even though this label has a QR code, a common solution is a traditional barcode.
Figure 1: Example of PCB label
Advantages of PCB traceability
PCB labels are crucial for traceability. They make it easier to track PCBs during operations such as production, assembly, and aftermarket distribution. This guarantees that parts move through the full production cycle and that the producer incorporates the correct components into products. In a broader sense, electronic PCB labeling enhances a company's management capabilities by boosting manufacturing effectiveness, warehouse management, maintenance, and spare parts service.
The capacity to follow the production process, identify defective parts, plan distribution logistics, provide customer service, and dispose of electronic components depends on the traceability information printed on printed circuit board labels.
In highly automated and digitized businesses, such as Smart Factories, traceability becomes crucial. A key component of "smart" manufacturing is the generation, analysis, and use of data by machines to optimize production processes. This boosts productivity and results in flexible manufacturing systems that can react rapidly and effectively to changes in demand. Only networked solutions that enable data transmission to or receipt from other supply chain systems are used by Industry 4.0 businesses.
A further benefit relates to data analysis. It is feasible to capture data straight from the production line, which can then be processed and analyzed (including using artificial intelligence techniques like machine learning) to increase the productivity of the manufacturing process.
The main advances in PCB traceability can be summarized as follows:
- Accurate part identification. When one part fails or is not working correctly, it is necessary to determine what other parts of the same type (or of the same production lot) might also be experiencing issues. This benefit mitigates the so-called “domino” effect
- Avoid performance issues. PCB traceability can also stop performance difficulties by spotting possible flaws before it's too late
- Improve quality control. PCB traceability makes it simpler for manufacturers to address quality control concerns and enhance the overall product quality by enabling them to pinpoint the source of any problems or faults that may develop throughout the production process
- Servicing and repairing. When performing maintenance or repairs, personnel may quickly find and replace defective components or pinpoint the cause of a problem thanks to PCB traceability, cutting downtime and increasing productivity
- Improved product reliability. Manufacturers can enhance the design or manufacturing process by tracing the production history of a PCB, resulting in better products and more customer satisfaction
- For some industries, like aircraft and medical equipment, regulatory organizations, and standards bodies frequently demand traceability. Manufacturers can show compliance with these rules and standards by using PCB traceability
- Liability protection. Manufacturers can be shielded from liability in the event of accidents or incidents by using PCB traceability to demonstrate that they have taken all required precautions to assure the safety and dependability of their goods
- Better defense against counterfeit electronic components or boards
- Integration with the Smart Factory system, with the additional possibility of using data analytics to extrapolate useful information on the improvement of the production process and product quality.
Technical solutions for traceability
PCB traceability is achieved using a variety of methods. Here are some of the most important ones:
- To make it simple to identify and track individual PCBs, barcodes can be printed and applied on the PCB or its packaging
- Using radio waves. Radio-frequency identification (RFID) tags can be inserted in PCBs or their packaging, allowing for automatic tracking and identification
- QR codes. Printing Quick Response (QR) codes on the PCB or its packaging allows manufacturers to add information like the PCB's serial number, manufacturing date, and more
- Laser marking. This technique provides permanent and highly readable marking by etching the identification data on a suitable label or directly onto the PCB or its components
- Data matrix codes. As they can hold more information in a smaller area than QR codes, which makes them perfect for PCB traceability
- Unique identifiers. Individual PCBs can be given unique identifiers, such as serial numbers or component numbers, to make it simple to monitor and identify them along the production and supply chain.
The choice of technique will depend on elements like the particular requirements of the industry, the size and complexity of the PCB, and the money available for execution. Each of these techniques has pros and cons.
Introducing surface-mount SMD components has allowed the automated assembly of printed circuit boards using SMT (Surface Mount Technology) assembly lines. This complex and sophisticated equipment manages the entire assembly line autonomously, taking the components from suitable feeders on which the component reels are placed and positioning them with extreme precision on the PCB using pick & place machines. While the PCB manufacturing process includes other stages (drilling, soldering, baking, optical and manual inspection, and more), component placement is one of the most critical.
Therefore, tracking of PCBs with printed labels shall be able to integrate with the SMT production line, managing the printed labels as if they were normal components (resistors, capacitors, integrated circuits, or transistors).
Figure 2 shows an SMT line with highlighted a feeder with pre-printed traceability labels. Treated as ordinary components, printed labels are picked from the pick & place machine and placed precisely in the assigned position on the PCB, then fed onto the processing line.
Figure 2: SMT production line with label feeder (Source: industryEMEA)
In addition to the equipment, an essential role is played by the materials used to manufacture the labels. Printability, resistance to heat, and chemical agents are the main factors that guide the choice of materials for labeling printed circuits. These labels contain information crucial to the manufacturing process which, if lost, can lead to profitability disruptions. To be sure that the labels placed on the printed circuit boards can withstand temperature fluctuations, mechanical abrasions, and the action of the chemicals used in the PCB production process, specific materials must be used.
The most commonly used material for these purposes is polyimide. Polyimide labels are suitable for high-density barcodes, data matrix codes, QR codes, and alphanumeric identification of printed circuit boards. Guaranteeing high stability over a wide range of temperatures (up to 300°C and beyond), this material allows printability with high resolution (i.e., 600 DPI) with a very small label size (see Figure 3).
Figure 3: 2D barcode labels with QR code and different sizes (Source: Link Hamson)Top of Form
Conclusion
PCB traceability is essential during manufacturing, assembly, and distribution operations, ensuring that components progress through the entire production cycle and that every single product is identifiable even after it leaves the factory. By integrating traceability, performed through labeling or other equivalent solutions, with other company processes, it is also possible to improve the management of a company structure and increase its production efficiency.
29.08.2023
and get your PCBA quote within the next 10 minutes!